Introduction/Background
Epoxy resins can be cured with a variety of compounds called curing agents which are also known as curatives, hardeners, or converters. Of the many classes/types of curing agents, amines are most widely utilized as curing agents in epoxy matrices for high performance composites. This produces a heteropolymer consisting of epoxy molecules linked together through the reactive sites of the curing agent. Usually when it is stated that an epoxy matrix is amine cured, it is meant that the curing agent(s) are primary amines which may be aromatic, cycloaliphatic (cyclic), or aliphatic primary amines. A primary amine has two active hydrogens that are each capable of reacting with an epoxy group. Most primary amine curing agents that are used have more than one primary amine per molecule so that crosslinking and therefore network development occur. A secondary amine will react with only one epoxy group. The reaction rate of the secondary amine with an epoxy resin is much slower than that of a primary amine. In contrast, tertiary amines which have no active hydrogens, will not react with epoxy resins but can cure epoxy resins catalytically, resulting in homopolymerization. Tertiary amines also accelerate the cure of primary and secondary amines with epoxy resins.
The reaction of a primary amine with an epoxy group produces both a secondary amine and secondary alcohol.

The secondary amine that is produced from this reaction can then react with another epoxy group producing a tertiary amine and another secondary alcohol.

Depending on the stoichiometry of amine to epoxy, there may also be further reaction of the secondary alcohols with epoxy groups producing an ether linkage. This is usually very limited in the resin system unless there is excess epoxy groups, a catalyst such as a tertiary amine, or high temperature cure. Even in these conditions the reaction rate is quite slow.
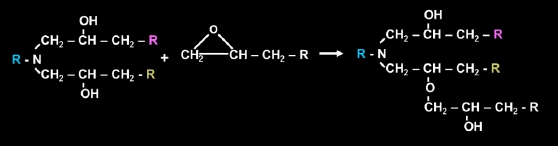
The above reactions are representative of amines with glycidyl ether, glycidyl ester, and glycidyl amine type epoxy resins but the overall reactivity of the amine epoxy system will also be a function of electronic and steric effects of the constituents. In most cases, the nucleophilicity of the amine dictates the reactivity with epoxy resins such that aliphatic amines>cycloaliphatic amines>aromatic amines. Accordingly, aliphatic amines can provide adequate cure of epoxy resins at room temperature whilearomatic amines require elevated temperature to effectively cure most epoxy resins. It should also be mentioned that catalysts can be added to increase the reaction rate of amines with epoxy resins but if used in excess oftentimes at the cost of a reduction in performance.
The amine curing agent selection depends on the desired mechanical and physical properties, environmental resistance, pot-life, viscosity, processing (liquid or solid), etc. In many formulated matrices, more than one amine type will be used to balance the processing and properties. Aromatic amines are often used as curing agents in epoxy prepreg resins as well as infusion resins, including those for resin transfer molding (RTM), vacuum assisted resin transfer molding (VARTM), resin film infusion (RFI), pultrusion, and filament winding. Cycloaliphatic amines are also used in VARTM type composite processes and specialty RTM and filament winding. Most commonly, cycloaliphatic and aliphatic amines are used as curing agents in epoxy wet-laminating resins. Shown below is a summary of some of the main advantages and disadvantages of the different classes of amine curing agents when used in epoxy systems. Please read all material safety data sheets (MSDS) before using the product.
ADVANTAGES Cycloaliphatic / Aliphatic Amine
|
DISADVANTAGES Cycloaliphatic / Aliphatic Amine
|
BSH-11/13 |